In many industries today, maintenance and performance studies for air-cooled heat exchangers still rely heavily on on-site inspections, leading to temporary and often incomplete datasets. This approach increases the risk of missing critical information, as it only captures a snapshot of the system’s condition at a specific point in time.
At Hexwise, we recognize that these gaps in data can result in delayed maintenance actions, inefficiencies, and suboptimal performance. That’s why our solution is built around two core pillars: Maintenance and Performance. By continuously monitoring key parameters in real time, we provide a complete and ongoing view of your air-cooled heat exchangers — empowering you to take proactive steps toward optimizing both reliability and performance.

Our solution
We are the world’s first digital twin software, specifically designed for Air-cooled heat exchangers, applicable to any industry, at any scale.
Together with our expert partners or your maintenance team, we equip your air-cooled heat exchangers with advanced sensors and gateways to continuously monitor their operation and performance.
The real-time data collected from the air-cooled heat exchanger is continuously streamed to our secure cloud, where it is processed in the digital twin model we have built for your system.
Our system analyses the incoming data. And it translates the data into relevant insights, allowing you to quickly identify inefficiencies and take corrective and preventive action.
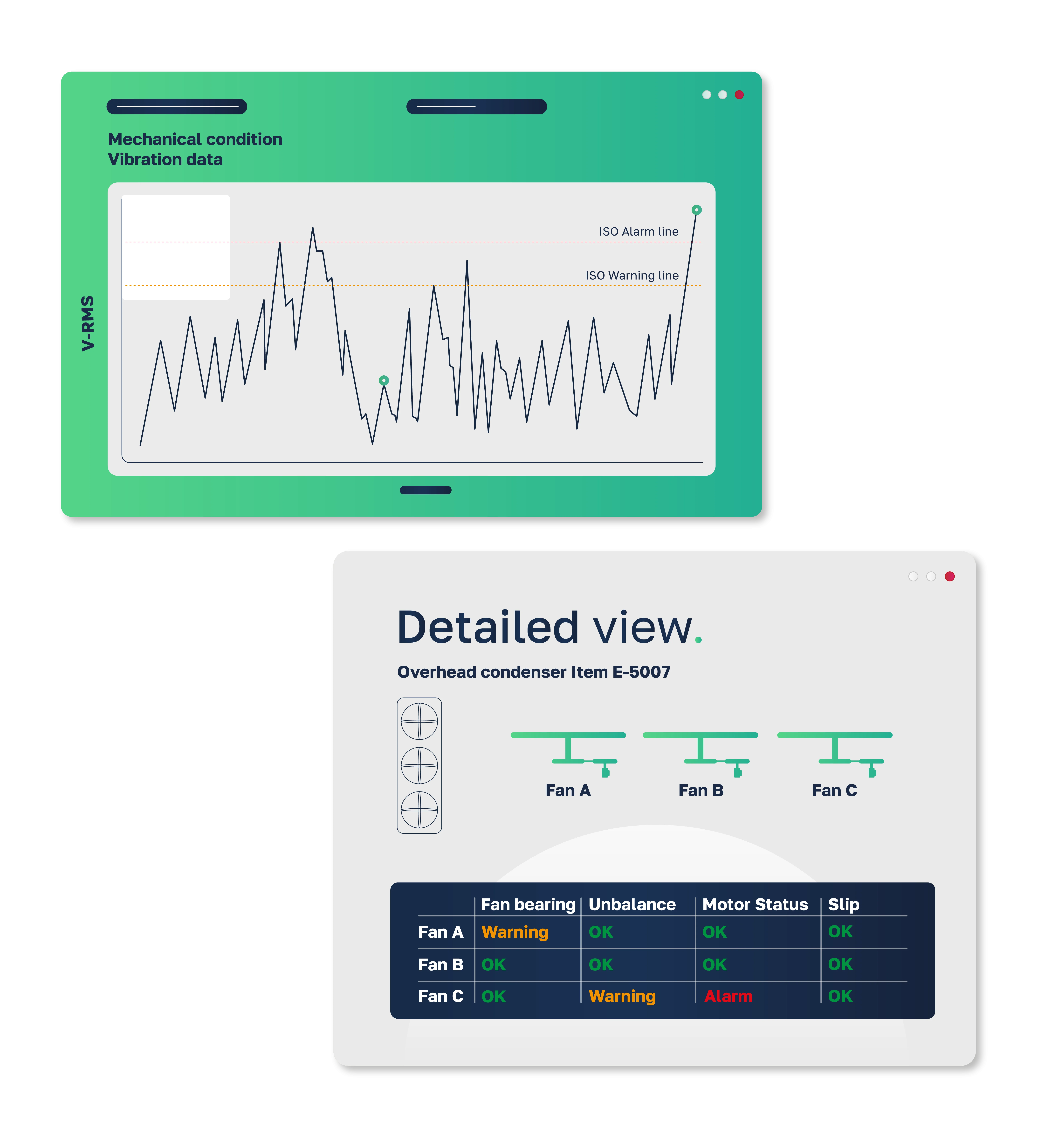
In the 1990s, few people believed they needed a navigation system in their car. Today, we can’t imagine driving without it. Similarly, we are now at a point where data-driven process optimization offers immense value —especially when it comes to maximizing cooling capacity. At Hexwise, our software is your navigation system to optimize the critical cooling capacity in your plant.
Process engineers from multiple leading global Fortune 500 energy and chemical companies have highlighted that “air-cooled heat exchangers are often seen as a known blind spot in the process industry,” with one senior engineer noting that “there’s always a feeling that data and information are missing from air-cooled heat exchangers compared to other process equipment.”
Additionally, production bottlenecks at certain locations for a large part of the year are directly attributed to “air-cooled heat exchanger cooling capacity shortages.”
At Hexwise, our digital twin technology is designed to address these critical issues by providing real-time data, optimizing performance, and ensuring more reliable and efficient operations.
